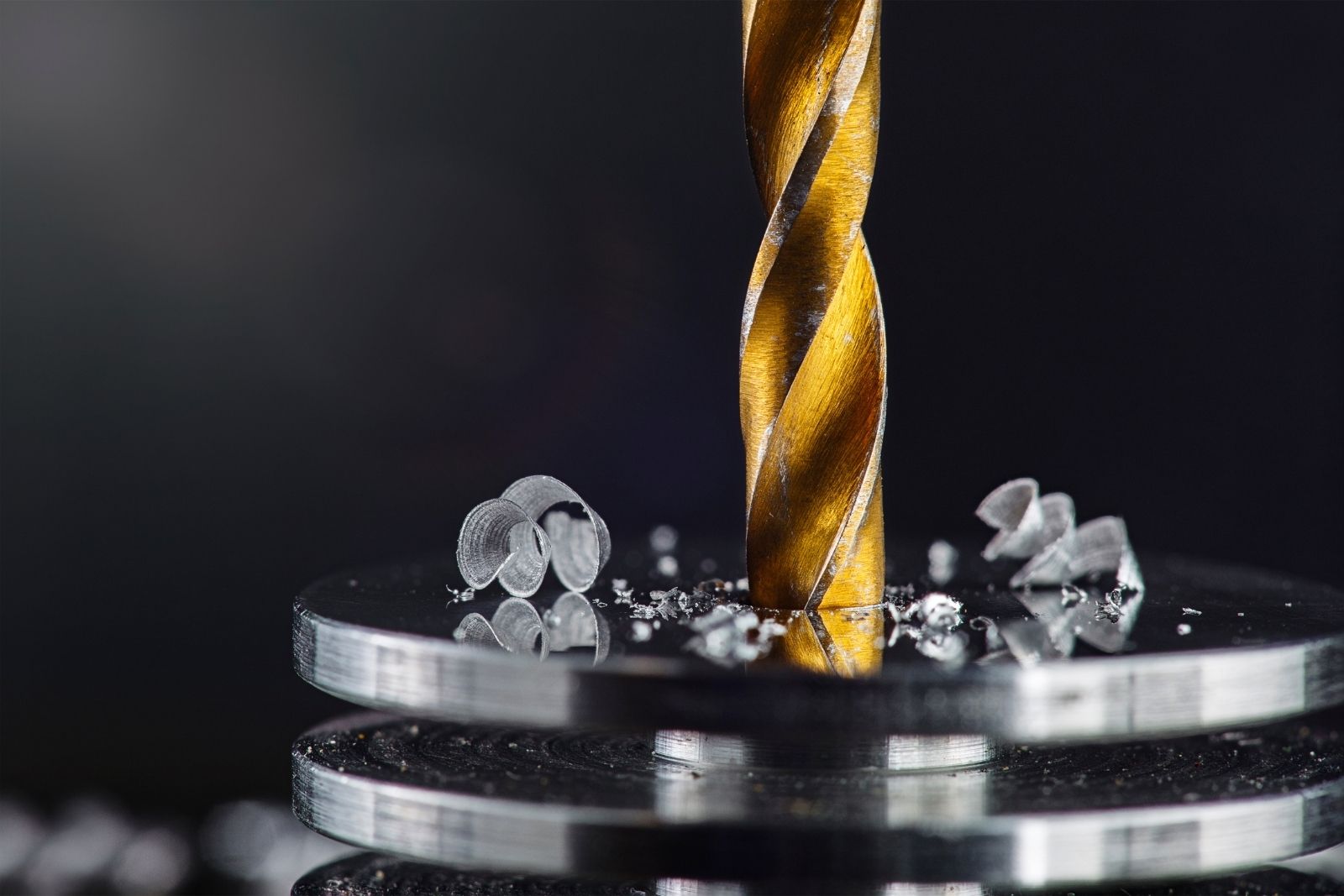
Chip removal: machining and equipment
The chip removal process is a fundamental process for the consequent passages of the production cycles. The removal of shavings can be declined in many industrial processes. It is important to understand how this process works as it allows you to be aware of when to go for the removal and the methodology to be adopted.
Table of Contents
1. When chip removal is needed
The seemingly insignificant issue of chip removal is actually a practical and very common problem. What are shavings? They are the metal (or wood) residues that are produced during the processing of a piece subjected to removal or perforation. Metal shavings are an inevitable material in the metalworking industry.
The removal process takes place mainly in two cases:
- It can only take place to complete the production process of the piece itself, when the piece, once the excess material (shavings) has been eliminated, can be sent to the customer (distributor, user, transformer, etc.);
- In other cases, the swarf removal operation is instead necessary before the piece is painted, machined or assembled. In addition, it happens that this piece requires a degreasing process, before being able to access the next stage of processing.
If the chips are not cleared in time, further flow of chips from the tool is blocked, causing newly formed chips to become entangled around the elements surrounding the tool and putting the operator and machine at risk.
2. Types of chips
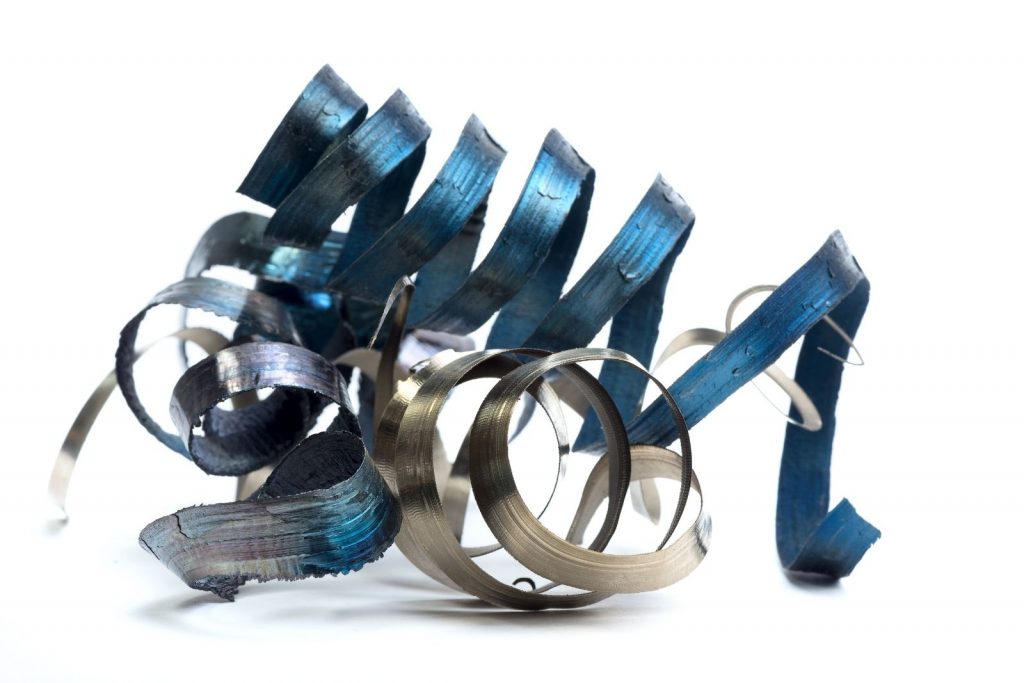
The various types of chips can be classified into three categories:
- Discontinuous chip: it is a small elementary chip whose detachment from the piece occurs before the formation of the next one has begun;
- Segmented chip: means a joined chip, but which has the part that crawls against the cutting face of the tool furrowed by more or less deep cracks;
- Flowing chip: means a continuous and uniform strip without splits.
3. Chip removal process
The machining for chip removal consists of a process in which the excess material is removed from a tool of greater hardness, or through the use of a manual or automatic mechanical force. The manufacturing process can be divided into two very specific phases:
- Roughing: in this phase, large quantities of material are removed in the shortest possible time. Roughing operations do not require particular precision;
- Finish: the final phase that brings the component to the specific requests. The finishing activity requires the utmost precision and constant attention from the staff in charge. Additional super-finishing and semi-finishing operations are required to achieve particularly high degrees of precision.
4. Types of processing for the removal of shavings
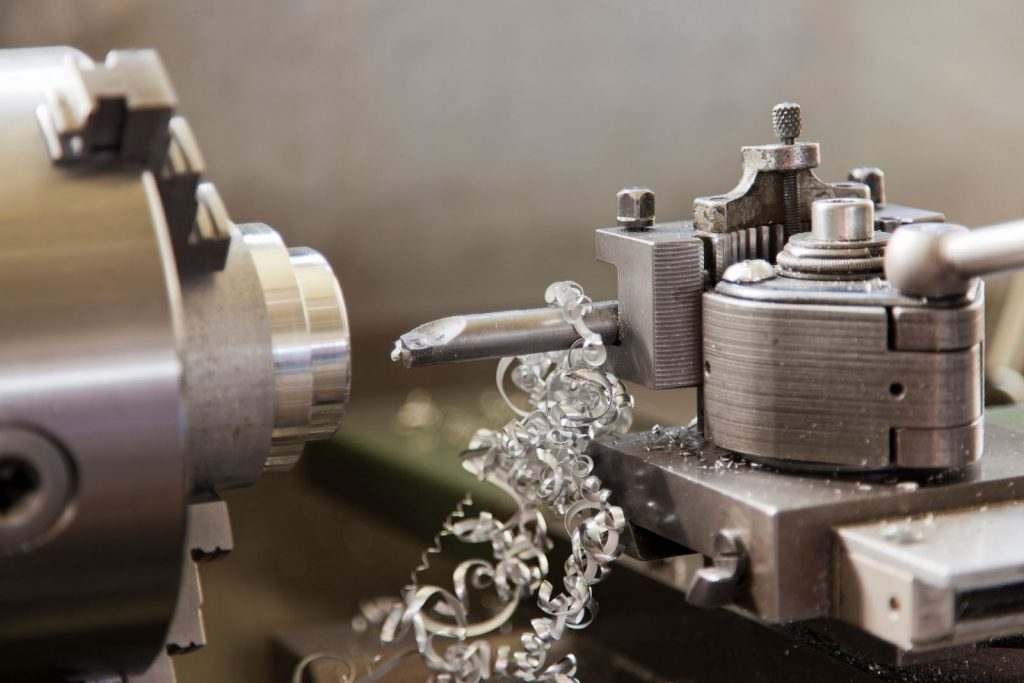
Chip removal, in most cases, requires well-defined industrial processes:
- Turning: is a machining process by chip removal in which a single-edged tool removes material from the surface of a rotating piece;
- Milling: it is an extremely versatile process, with medium-low productivity, which requires professional and specialized labor;
- Grinding: production process aimed at eliminating any deformations, with high processing precision and a considerable degree of surface finish. It is an expensive process that requires skill and specialization;
- Drilling: Drilling is a process that is used to create a circular hole in a piece and is generally performed with a cylindrical rotating tool with two cutting edges on the face and is called a drill.
5. Automatic parts washers based on heated water
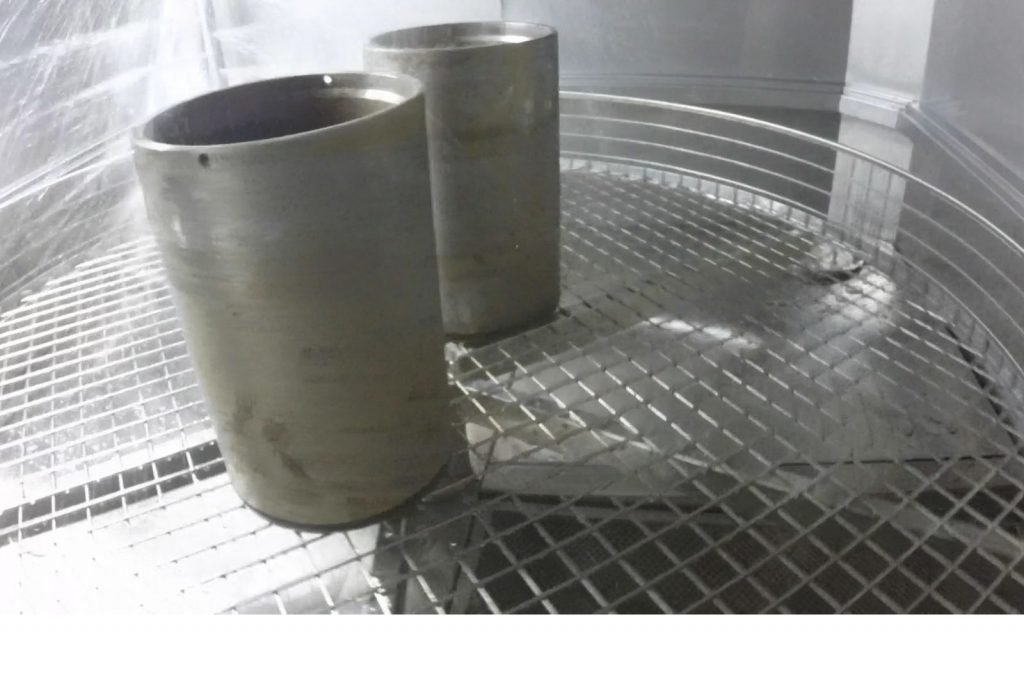
In some cases the piece needs a simple removal with the aid of a mechanical force. In these cases, where perhaps the daily production does not exceed thousands of units, automatic rotary basket machines can be an excellent solution. These machines (washers) allow to solve the chip removal of a few thousand units with a single washing cycle and also to implement the degreasing of the piece thanks to the same cycle.
The washers are automatic parts washers based on heated water. The machine is commonly called a washing machine, as its process and functionality reminds us of the well-known household appliance. The Washer has a basket where you can place the pieces (in some cases the basket can be reinforced or made to doc in order to contain even the smallest pieces). At the base, above and to the side of this basket there are washing ramps which, thanks to the aid of a double impeller pump in Aisi 304 stainless steel, deliver the washing product previously heated to high pressure (the power expressed in bar varies from machine to machine). 360 ° cleaning is guaranteed by the fact that the drum performs continuous rotations during the washing cycle.
6. Manual equipment
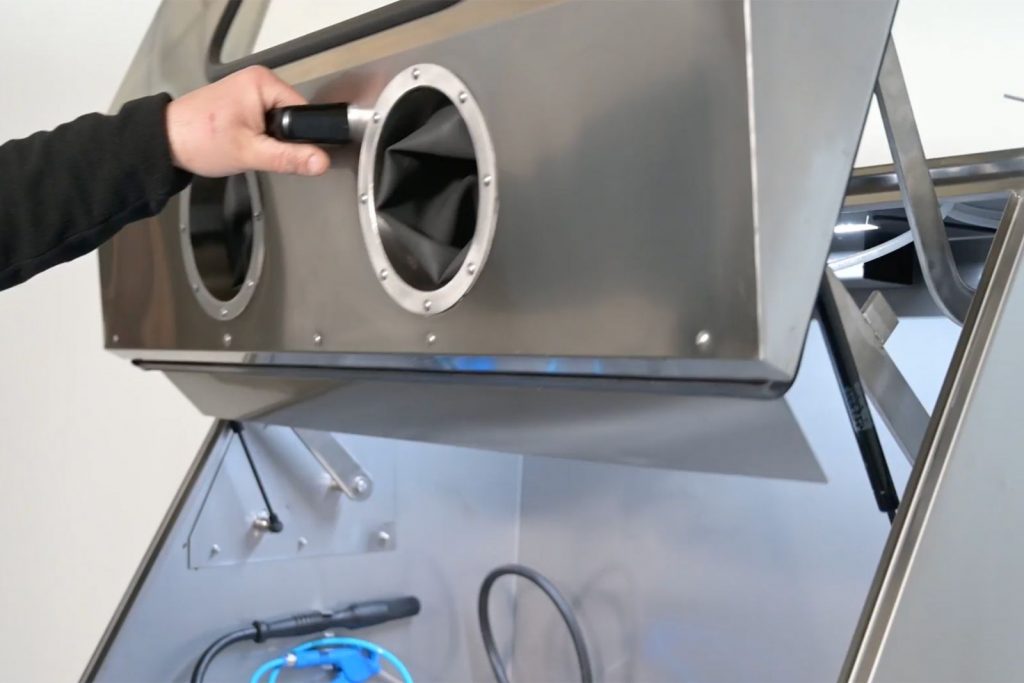
In other cases, the removal of chips or excess material requires a more complex and precise machining. In this case it is a question of daily productions that hardly exceed hundreds of units per day.
In these particular cases, where both the degreasing and removal action requires the supervision of the human eye, we recommend high pressure manual equipment (eco and Top High pressure). These machines always use a heated water-based cleaning product, but dispensing is done manually via a nozzle powered by a high-pressure electric pump.
7. The removal of shavings: a precise and necessary cleaning
Chip removal is a process in which a piece is shaped using tools that can remove excess material. This machining process allows to obtain degrees of surface finish and dimensional accuracy of the metal pieces, especially when the shape is complex and cannot be implemented effectively with other technologies. The type of processing can vary according to the needs, automatic parts washers or high pressure manual equipment can be used.